Characteristics of commercial white LED lamps for commercial white LED lamps 1. Introduction The luminous efficiency of LEDs is increasing, making high-power white LEDs gradually accepted as solid-state lighting sources. With the advancement and development of lighting technology, Improving lighting quality, improving lighting technology, making lighting economically reasonable, safe to use, saving energy, and protecting the environment are the key research projects of the international and domestic lighting engineering industry [1]. In 1996, Nichia Corporation realized the commercialization of white LEDs, which were composed of a blue LED chip and a yellow phosphor doped with Ce3+. White LEDs play an important role in display and signal indication, such as LED displays, car lights and traffic lights [2, 3].
[Source: "High - tech LED - Technology and Applications" December issue ]
1 Introduction
The luminous efficiency of light-emitting diode (LED) chips continues to increase, making high-power white LEDs gradually accepted as solid-state lighting sources. With the advancement and development of lighting technology, improving lighting quality, improving lighting technology, making lighting economical and safe to use, Saving energy and protecting the environment are the key research topics for the international and domestic lighting engineering industry. In 1996, Nichia Corporation realized the commercialization of white LEDs, which were composed of a blue LED chip and a yellow phosphor doped with Ce3+. White LEDs play an important role in display and signal indication, such as LED displays, car lights and traffic lights.
1 Introduction
The luminous efficiency of light-emitting diode (LED) chips continues to increase, making high-power white LEDs gradually accepted as solid-state lighting sources. With the advancement and development of lighting technology, improving lighting quality, improving lighting technology, making lighting economical and safe to use, Saving energy and protecting the environment are the key research topics for the international and domestic lighting engineering industry. In 1996, Nichia Corporation realized the commercialization of white LEDs, which were composed of a blue LED chip and a yellow phosphor doped with Ce3+. White LEDs play an important role in display and signal indication, such as LED displays, car lights and traffic lights.
The country is paying more and more attention to lighting energy conservation and environmental protection issues, and has been vigorously promoting the use of LED lights. LED light source has outstanding features such as no stroboscopic, low energy consumption, impact resistance, environmental protection and long life. Therefore, various countries and regions are rushing to invest in the development of white LED lighting sources. However, there are still many problems to be solved for power LEDs for lighting: currently white LEDs generally use blue LEDs to excite yellow phosphors to synthesize white light, and there is a problem that the color rendering index of LED lamps with high color temperature is low. Since the illumination source has higher brightness requirements than the display light source, the white LED power should be as large as possible. However, during high current operation, as the working time increases, the LED itself decays, and the phosphor and packaging materials deteriorate. The cause is a decrease in luminous flux. With the large increase in power, the heat generation of the PN junction is greatly improved, and this part of heat directly affects the operating temperature, luminous efficiency, luminescence spectrum, and lifetime reliability of the LED. The performance of high-power white LED products can be improved by adjusting the ratio of phosphor to silica gel, the amount of dispensing and the amount of thermal paste, the choice of packaging materials, the design of the light distribution curve and the improvement of power conversion efficiency. Many researchers have done a lot of research on the performance of LED chips, but there are few studies on the characteristics of commercial high-power white LED lamps. Therefore, this paper studies the effects of temperature changes of different packaging materials on the color-electric properties of high-power white LED lamps.
2. Experimental process
The object studied in this experiment is a 3W high power white LED lamp. The device includes: (1) 1W blue chip produced by Taiwan Jingyuan Optoelectronics Co., Ltd. (Specification: 45×45mil); (2) Silica gel produced by Dow Corning; (3) Hemispherical hollow lens of PC material; (4) Copper substrate (model: copper T1) and aluminum substrate (model: aluminum alloy 6063l); (5) cylindrical aluminum heat sink (specification: No. 1 Φ30mm × H47mm; No. 2 Φ45mm × H54mm); (6) Ce3+-doped Yttrium aluminum garnet (YAG) phosphor.
The object studied in this experiment is a 3W high power white LED lamp. The device includes: (1) 1W blue chip produced by Taiwan Jingyuan Optoelectronics Co., Ltd. (Specification: 45×45mil); (2) Silica gel produced by Dow Corning; (3) Hemispherical hollow lens of PC material; (4) Copper substrate (model: copper T1) and aluminum substrate (model: aluminum alloy 6063l); (5) cylindrical aluminum heat sink (specification: No. 1 Φ30mm × H47mm; No. 2 Φ45mm × H54mm); (6) Ce3+-doped Yttrium aluminum garnet (YAG) phosphor.
Figure 1 shows a schematic (a) and a cross-sectional view (b) of a high power white LED lamp. Wherein T in Figure 1(b) indicates the position of the thermocouple.
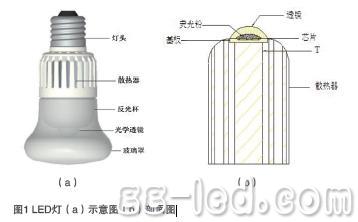
First, an automatic wire bonding machine is used to weld three chips on the aluminum substrate and the copper substrate (in a "product" type arrangement in series), and the silica gel is coated on the soldered chip to be solidified. Then, the silica gel and the YAG phosphor were mixed in a certain ratio, stirred for 10 minutes, vacuumed for 30 minutes, and then coated on the cured silica gel, wherein the curing conditions were both 150 ° C and baked for 1 h. Then, the substrate is mounted on a heat sink with a thermal paste applied therebetween. A lens and glass cover mounted on the phosphor layer can be used to control light distribution and prevent glare. When driven by a constant current source, the blue light emitted by the chip excites the phosphor, and finally a uniform white light can be seen through the lens and the glass cover.
Unfinished
For more information, please refer to "High - tech LED - Technology and Applications" December issue
The integrating sphere is also called a spherical photometer. It is a complete spherical shell with an inner hollow and a white diffuse reflective layer on the inner wall. The test system is calibrated with a standard halogen lamp. The light source is placed in the integrating sphere. A part of the light emitted by the light source and diffusely reflected by the spherical surface is incident on the light detector through the window on the wall of the ball. After the light is collected, the light is collected by the detector. The signal is converted into a photocurrent signal. After being sampled and amplified, it is converted into a digital signal by A/D and sent to the microprocessor. Then, the total luminous flux Φ (lm) and luminous efficiency η (lm/W) are obtained by calculation. Characteristics of commercial white LED lamps 1. Introduction The luminous efficiency of light-emitting diode (LED) chips is increasing, making high-power white LEDs gradually accepted as solid-state lighting sources. With the advancement and development of lighting technology, lighting quality is improved and lighting is improved. Technology, making lighting economical, safe use, energy conservation, and environmental protection is a key research topic in the international and domestic lighting engineering industry [1]. In 1996, Nichia Corporation realized the commercialization of white LEDs, which were composed of a blue LED chip and a yellow phosphor doped with Ce3+. White LEDs play an important role in display and signal indication, such as LED displays, car lights and traffic lights [2, 3].
The country is paying more and more attention to lighting energy conservation and environmental protection issues, and has been vigorously promoting the use of LED lights. LED light source has outstanding features such as no stroboscopic, low energy consumption, impact resistance, environmental protection and long life. Therefore, various countries and regions are rushing to invest in the development of white LED lighting sources. However, there are still many problems to be solved for power LEDs for lighting: currently white LEDs generally use blue LEDs to excite yellow phosphors to synthesize white light, and there is a problem that the color rendering index of LED lamps with high color temperature is low. Since the illumination source has higher brightness requirements than the display light source, the white LED power should be as large as possible. However, during high current operation, as the working time increases, the LED itself decays, and the phosphor and packaging materials deteriorate. The cause is a decrease in luminous flux. With the large increase in power, the heat generation of the PN junction is greatly improved, and this part of the heat directly affects the operating temperature, luminous efficiency, luminescence spectrum, and lifetime reliability of the LED [4, 5]. . The performance of high-power white LED products can be improved by adjusting the ratio of phosphor to silica gel, the amount of dispensing and the amount of thermal paste, the choice of packaging materials, the design of the light distribution curve and the improvement of power conversion efficiency. Many researchers have done a lot of research on the performance of LED chips, but there are few studies on the characteristics of commercial high-power white LED lamps. Therefore, this paper studies the effects of temperature changes of different packaging materials on the color-electric properties of high-power white LED lamps.
2. Experimental procedure The object studied in this experiment is a 3W high power white LED lamp. The device includes: (1) 1W blue chip produced by Taiwan Jingyuan Optoelectronics Co., Ltd. (Specification: 45×45mil); (2) Silica gel produced by Dow Corning; (3) Hemispherical hollow lens of PC material; (4) Copper substrate (model: copper T1) and aluminum substrate (model: aluminum alloy 6063l); (5) cylindrical aluminum heat sink (specification: No. 1 Φ30mm × H47mm; No. 2 Φ45mm × H54mm); (6) Ce3+-doped Yttrium aluminum garnet (YAG) phosphor.
Figure 1 shows a schematic (a) and a cross-sectional view (b) of a high power white LED lamp. Wherein T in Figure 1(b) indicates the position of the thermocouple.
First, an automatic wire bonding machine is used to weld three chips on the aluminum substrate and the copper substrate (in a "product" type arrangement in series), and the silica gel is coated on the soldered chip to be solidified. Then, the silica gel and the YAG phosphor were mixed in a certain ratio, stirred for 10 minutes, vacuumed for 30 minutes, and then coated on the cured silica gel, wherein the curing conditions were both 150 ° C and baked for 1 h. Then, the substrate is mounted on a heat sink with a thermal paste applied therebetween. A lens and glass cover mounted on the phosphor layer can be used to control light distribution and prevent glare. When driven by a constant current source, the blue light emitted by the chip excites the phosphor, and finally a uniform white light can be seen through the lens and the glass cover.
The integrating sphere is also called a spherical photometer. It is a complete spherical shell with an inner hollow and a white diffuse reflective layer on the inner wall. The test system is calibrated with a standard halogen lamp. The light source is placed in the integrating sphere. A part of the light emitted by the light source and diffusely reflected by the spherical surface is incident on the light detector through the window on the wall of the ball. After the light is collected, the light is collected by the detector. The signal is converted into a photocurrent signal. After being sampled and amplified, it is converted into a digital signal by A/D and sent to the microprocessor. Then, the total luminous flux Φ (lm) and luminous efficiency η (lm/W) are obtained by calculation. Characteristics of commercial white LED lamps 1. Introduction The luminous efficiency of light-emitting diode (LED) chips is increasing, making high-power white LEDs gradually accepted as solid-state lighting sources. With the advancement and development of lighting technology, lighting quality is improved and lighting is improved. Technology, making lighting economical, safe use, energy conservation, and environmental protection is a key research topic in the international and domestic lighting engineering industry [1]. In 1996, Nichia Corporation realized the commercialization of white LEDs, which were composed of a blue LED chip and a yellow phosphor doped with Ce3+. White LEDs play an important role in display and signal indication, such as LED displays, car lights and traffic lights [2, 3].
The country is paying more and more attention to lighting energy conservation and environmental protection issues, and has been vigorously promoting the use of LED lights. LED light source has outstanding features such as no stroboscopic, low energy consumption, impact resistance, environmental protection and long life. Therefore, various countries and regions are rushing to invest in the development of white LED lighting sources. However, there are still many problems to be solved for power LEDs for lighting: currently white LEDs generally use blue LEDs to excite yellow phosphors to synthesize white light, and there is a problem that the color rendering index of LED lamps with high color temperature is low. Since the illumination source has higher brightness requirements than the display light source, the white LED power should be as large as possible. However, during high current operation, as the working time increases, the LED itself decays, and the phosphor and packaging materials deteriorate. The cause is a decrease in luminous flux. With the large increase in power, the heat generation of the PN junction is greatly improved, and this part of the heat directly affects the operating temperature, luminous efficiency, luminescence spectrum, and lifetime reliability of the LED [4, 5]. . The performance of high-power white LED products can be improved by adjusting the ratio of phosphor to silica gel, the amount of dispensing and the amount of thermal paste, the choice of packaging materials, the design of the light distribution curve and the improvement of power conversion efficiency. Many researchers have done a lot of research on the performance of LED chips, but there are few studies on the characteristics of commercial high-power white LED lamps. Therefore, this paper studies the effects of temperature changes of different packaging materials on the color-electric properties of high-power white LED lamps.
2. Experimental procedure The object studied in this experiment is a 3W high power white LED lamp. The device includes: (1) 1W blue chip produced by Taiwan Jingyuan Optoelectronics Co., Ltd. (Specification: 45×45mil); (2) Silica gel produced by Dow Corning; (3) Hemispherical hollow lens of PC material; (4) Copper substrate (model: copper T1) and aluminum substrate (model: aluminum alloy 6063l); (5) cylindrical aluminum heat sink (specification: No. 1 Φ30mm × H47mm; No. 2 Φ45mm × H54mm); (6) Ce3+-doped Yttrium aluminum garnet (YAG) phosphor.
Figure 1 shows a schematic (a) and a cross-sectional view (b) of a high power white LED lamp. Wherein T in Figure 1(b) indicates the position of the thermocouple.
First, an automatic wire bonding machine is used to weld three chips on the aluminum substrate and the copper substrate (in a "product" type arrangement in series), and the silica gel is coated on the soldered chip to be solidified. Then, the silica gel and the YAG phosphor were mixed in a certain ratio, stirred for 10 minutes, vacuumed for 30 minutes, and then coated on the cured silica gel, wherein the curing conditions were both 150 ° C and baked for 1 h. Then, the substrate is mounted on a heat sink with a thermal paste applied therebetween. A lens and glass cover mounted on the phosphor layer can be used to control light distribution and prevent glare. When driven by a constant current source, the blue light emitted by the chip excites the phosphor, and finally a uniform white light can be seen through the lens and the glass cover.
The integrating sphere is also called a spherical photometer. It is a complete spherical shell with an inner hollow and a white diffuse reflective layer on the inner wall. The test system is calibrated with a standard halogen lamp. The light source is placed in the integrating sphere. A part of the light emitted by the light source and diffusely reflected by the spherical surface is incident on the light detector through the window on the wall of the ball. After the light is collected, the light is collected by the detector. The signal is converted into a photocurrent signal. After being sampled and amplified, it is converted into a digital signal by A/D and sent to the microprocessor. Then, the total luminous flux Φ (lm) and luminous efficiency η (lm/W) are obtained by calculation. Characteristics of commercial white LED lamps 1. Introduction The luminous efficiency of light-emitting diode (LED) chips is increasing, making high-power white LEDs gradually accepted as solid-state lighting sources. With the advancement and development of lighting technology, lighting quality is improved and lighting is improved. Technology, making lighting economical, safe use, energy conservation, and environmental protection is a key research topic in the international and domestic lighting engineering industry [1]. In 1996, Nichia Corporation realized the commercialization of white LEDs, which were composed of a blue LED chip and a yellow phosphor doped with Ce3+. White LEDs play an important role in display and signal indication, such as LED displays, car lights and traffic lights [2, 3].
The country is paying more and more attention to lighting energy conservation and environmental protection issues, and has been vigorously promoting the use of LED lights. LED light source has outstanding features such as no stroboscopic, low energy consumption, impact resistance, environmental protection and long life. Therefore, various countries and regions are rushing to invest in the development of white LED lighting sources. However, there are still many problems to be solved for power LEDs for lighting: currently white LEDs generally use blue LEDs to excite yellow phosphors to synthesize white light, and there is a problem that the color rendering index of LED lamps with high color temperature is low. Since the illumination source has higher brightness requirements than the display light source, the white LED power should be as large as possible. However, during high current operation, as the working time increases, the LED itself decays, and the phosphor and packaging materials deteriorate. The cause is a decrease in luminous flux. With the large increase in power, the heat generation of the PN junction is greatly improved, and this part of the heat directly affects the operating temperature, luminous efficiency, luminescence spectrum, and lifetime reliability of the LED [4, 5]. . The performance of high-power white LED products can be improved by adjusting the ratio of phosphor to silica gel, the amount of dispensing and the amount of thermal paste, the choice of packaging materials, the design of the light distribution curve and the improvement of power conversion efficiency. Many researchers have done a lot of research on the performance of LED chips, but there are few studies on the characteristics of commercial high-power white LED lamps. Therefore, this paper studies the effects of temperature changes of different packaging materials on the color-electric properties of high-power white LED lamps.
2. Experimental procedure The object studied in this experiment is a 3W high power white LED lamp. The device includes: (1) 1W blue chip produced by Taiwan Jingyuan Optoelectronics Co., Ltd. (Specification: 45×45mil); (2) Silica gel produced by Dow Corning; (3) Hemispherical hollow lens of PC material; (4) Copper substrate (model: copper T1) and aluminum substrate (model: aluminum alloy 6063l); (5) cylindrical aluminum heat sink (specification: No. 1 Φ30mm × H47mm; No. 2 Φ45mm × H54mm); (6) Ce3+-doped Yttrium aluminum garnet (YAG) phosphor.
Figure 1 shows a schematic (a) and a cross-sectional view (b) of a high power white LED lamp. Wherein T in Figure 1(b) indicates the position of the thermocouple.
First, an automatic wire bonding machine is used to weld three chips on the aluminum substrate and the copper substrate (in a "product" type arrangement in series), and the silica gel is coated on the soldered chip to be solidified. Then, the silica gel and the YAG phosphor were mixed in a certain ratio, stirred for 10 minutes, vacuumed for 30 minutes, and then coated on the cured silica gel, wherein the curing conditions were both 150 ° C and baked for 1 h. Then, the substrate is mounted on a heat sink with a thermal paste applied therebetween. A lens and glass cover mounted on the phosphor layer can be used to control light distribution and prevent glare. When driven by a constant current source, the blue light emitted by the chip excites the phosphor, and finally a uniform white light can be seen through the lens and the glass cover.
The integrating sphere is also called a spherical photometer. It is a complete spherical shell with an inner hollow and a white diffuse reflective layer on the inner wall. The test system is calibrated with a standard halogen lamp. The light source is placed in the integrating sphere. A part of the light emitted by the light source and diffusely reflected by the spherical surface is incident on the light detector through the window on the wall of the ball. After the light is collected, the light is collected by the detector. The signal is converted into a photocurrent signal. After being sampled and amplified, it is converted into a digital signal by A/D and sent to the microprocessor. Then, the total luminous flux Φ (lm) and luminous efficiency η (lm/W) are obtained by calculation. Characteristics of commercial white LED lamps 1. Introduction The luminous efficiency of light-emitting diode (LED) chips is increasing, making high-power white LEDs gradually accepted as solid-state lighting sources. With the advancement and development of lighting technology, lighting quality is improved and lighting is improved. Technology, making lighting economical, safe use, energy conservation, and environmental protection is a key research topic in the international and domestic lighting engineering industry [1]. In 1996, Nichia Corporation realized the commercialization of white LEDs, which were composed of a blue LED chip and a yellow phosphor doped with Ce3+. White LEDs play an important role in display and signal indication, such as LED displays, car lights and traffic lights [2, 3].
The country is paying more and more attention to lighting energy conservation and environmental protection issues, and has been vigorously promoting the use of LED lights. LED light source has outstanding features such as no stroboscopic, low energy consumption, impact resistance, environmental protection and long life. Therefore, various countries and regions are rushing to invest in the development of white LED lighting sources. However, there are still many problems to be solved for power LEDs for lighting: currently white LEDs generally use blue LEDs to excite yellow phosphors to synthesize white light, and there is a problem that the color rendering index of LED lamps with high color temperature is low. Since the illumination source has higher brightness requirements than the display light source, the white LED power should be as large as possible. However, during high current operation, as the working time increases, the LED itself decays, and the phosphor and packaging materials deteriorate. The cause is a decrease in luminous flux. With the large increase in power, the heat generation of the PN junction is greatly improved, and this part of the heat directly affects the operating temperature, luminous efficiency, luminescence spectrum, and lifetime reliability of the LED [4, 5]. . The performance of high-power white LED products can be improved by adjusting the ratio of phosphor to silica gel, the amount of dispensing and the amount of thermal paste, the choice of packaging materials, the design of the light distribution curve and the improvement of power conversion efficiency. Many researchers have done a lot of research on the performance of LED chips, but there are few studies on the characteristics of commercial high-power white LED lamps. Therefore, this paper studies the effects of temperature changes of different packaging materials on the color-electric properties of high-power white LED lamps.
2. Experimental procedure The object studied in this experiment is a 3W high power white LED lamp. The device includes: (1) 1W blue chip produced by Taiwan Jingyuan Optoelectronics Co., Ltd. (Specification: 45×45mil); (2) Silica gel produced by Dow Corning; (3) Hemispherical hollow lens of PC material; (4) Copper substrate (model: copper T1) and aluminum substrate (model: aluminum alloy 6063l); (5) cylindrical aluminum heat sink (specification: No. 1 Φ30mm × H47mm; No. 2 Φ45mm × H54mm); (6) Ce3+-doped Yttrium aluminum garnet (YAG) phosphor.
Figure 1 shows a schematic (a) and a cross-sectional view (b) of a high power white LED lamp. Wherein T in Figure 1(b) indicates the position of the thermocouple.
First, an automatic wire bonding machine is used to weld three chips on the aluminum substrate and the copper substrate (in a "product" type arrangement in series), and the silica gel is coated on the soldered chip to be solidified. Then, the silica gel and the YAG phosphor were mixed in a certain ratio, stirred for 10 minutes, vacuumed for 30 minutes, and then coated on the cured silica gel, wherein the curing conditions were both 150 ° C and baked for 1 h. Then, the substrate is mounted on a heat sink with a thermal paste applied therebetween. A lens and glass cover mounted on the phosphor layer can be used to control light distribution and prevent glare. When driven by a constant current source, the blue light emitted by the chip excites the phosphor, and finally a uniform white light can be seen through the lens and the glass cover.
The integrating sphere is also called a spherical photometer. It is a complete spherical shell with an inner hollow and a white diffuse reflective layer on the inner wall. The test system is calibrated with a standard halogen lamp. The light source is placed in the integrating sphere. A part of the light emitted by the light source and diffusely reflected by the spherical surface is incident on the light detector through the window on the wall of the ball. After the light is collected, the light is collected by the detector. The signal is converted into a photocurrent signal. After being sampled and amplified, it is converted into a digital signal by A/D and sent to the microprocessor. Then, the total luminous flux Φ (lm) and luminous efficiency η (lm/W) are obtained by calculation.
The integrating sphere is also called a spherical photometer. It is a complete spherical shell with an inner hollow and a white diffuse reflective layer on the inner wall. The test system is calibrated with a standard halogen lamp. The light source is placed in the integrating sphere. A part of the light emitted by the light source and diffusely reflected by the spherical surface is incident on the light detector through the window on the wall of the ball. After the light is collected, the light is collected by the detector. The signal is converted into a photocurrent signal. After being sampled and amplified, it is converted into a digital signal by A/D and sent to the microprocessor. Then, the total luminous flux Φ (lm) and luminous efficiency η (lm/W) are obtained by calculation. Sexual research 1. Introduction The luminous efficiency of light-emitting diode (LED) chips is increasing, making high-power white LEDs gradually accepted as solid-state lighting sources. With the advancement and development of lighting technology, improving lighting quality, improving lighting technology, and making lighting economy Reasonable, safe use, energy conservation, and environmental protection are the key research projects of the international and domestic lighting engineering industry [1]. In 1996, Nichia Corporation realized the commercialization of white LEDs, which were composed of a blue LED chip and a yellow phosphor doped with Ce3+. White LEDs play an important role in display and signal indication, such as LED displays, car lights and traffic lights [2, 3].
The country is paying more and more attention to lighting energy conservation and environmental protection issues, and has been vigorously promoting the use of LED lights. LED light source has outstanding features such as no stroboscopic, low energy consumption, impact resistance, environmental protection and long life. Therefore, various countries and regions are rushing to invest in the development of white LED lighting sources. However, there are still many problems to be solved for power LEDs for lighting: currently white LEDs generally use blue LEDs to excite yellow phosphors to synthesize white light, and there is a problem that the color rendering index of LED lamps with high color temperature is low. Since the illumination source has higher brightness requirements than the display light source, the white LED power should be as large as possible. However, during high current operation, as the working time increases, the LED itself decays, and the phosphor and packaging materials deteriorate. The cause is a decrease in luminous flux. With the large increase in power, the heat generation of the PN junction is greatly improved, and this part of the heat directly affects the operating temperature, luminous efficiency, luminescence spectrum, and lifetime reliability of the LED [4, 5]. . The performance of high-power white LED products can be improved by adjusting the ratio of phosphor to silica gel, the amount of dispensing and the amount of thermal paste, the choice of packaging materials, the design of the light distribution curve and the improvement of power conversion efficiency. Many researchers have done a lot of research on the performance of LED chips, but there are few studies on the characteristics of commercial high-power white LED lamps. Therefore, this paper studies the effects of temperature changes of different packaging materials on the color-electric properties of high-power white LED lamps.
2. Experimental procedure The object studied in this experiment is a 3W high power white LED lamp. The device includes: (1) 1W blue chip produced by Taiwan Jingyuan Optoelectronics Co., Ltd. (Specification: 45×45mil); (2) Silica gel produced by Dow Corning; (3) Hemispherical hollow lens of PC material; (4) Copper substrate (model: copper T1) and aluminum substrate (model: aluminum alloy 6063l); (5) cylindrical aluminum heat sink (specification: No. 1 Φ30mm × H47mm; No. 2 Φ45mm × H54mm); (6) Ce3+-doped Yttrium aluminum garnet (YAG) phosphor.
Figure 1 shows a schematic (a) and a cross-sectional view (b) of a high power white LED lamp. Wherein T in Figure 1(b) indicates the position of the thermocouple.
First, an automatic wire bonding machine is used to weld three chips on the aluminum substrate and the copper substrate (in a "product" type arrangement in series), and the silica gel is coated on the soldered chip to be solidified. Then, the silica gel and the YAG phosphor were mixed in a certain ratio, stirred for 10 minutes, vacuumed for 30 minutes, and then coated on the cured silica gel, wherein the curing conditions were both 150 ° C and baked for 1 h. Then, the substrate is mounted on a heat sink with a thermal paste applied therebetween. A lens and glass cover mounted on the phosphor layer can be used to control light distribution and prevent glare. When driven by a constant current source, the blue light emitted by the chip excites the phosphor, and finally a uniform white light can be seen through the lens and the glass cover.
The integrating sphere is also called a spherical photometer. It is a complete spherical shell with an inner hollow and a white diffuse reflective layer on the inner wall. The test system is calibrated with a standard halogen lamp. The light source is placed in the integrating sphere. A part of the light emitted by the light source and diffusely reflected by the spherical surface is incident on the light detector through the window on the wall of the ball. After the light is collected, the light is collected by the detector. The signal is converted into a photocurrent signal. After being sampled and amplified, it is converted into a digital signal by A/D and sent to the microprocessor. Then, the total luminous flux Φ (lm) and luminous efficiency η (lm/W) are obtained by calculation. Characteristics of commercial white LED lamps 1. Introduction The luminous efficiency of light-emitting diode (LED) chips is increasing, making high-power white LEDs gradually accepted as solid-state lighting sources. With the advancement and development of lighting technology, lighting quality is improved and lighting is improved. Technology, making lighting economical, safe use, energy conservation, and environmental protection is a key research topic in the international and domestic lighting engineering industry [1]. In 1996, Nichia Corporation realized the commercialization of white LEDs, which were composed of a blue LED chip and a yellow phosphor doped with Ce3+. White LEDs play an important role in display and signal indication, such as LED displays, car lights and traffic lights [2, 3].
The country is paying more and more attention to lighting energy conservation and environmental protection issues, and has been vigorously promoting the use of LED lights. LED light source has outstanding features such as no stroboscopic, low energy consumption, impact resistance, environmental protection and long life. Therefore, various countries and regions are rushing to invest in the development of white LED lighting sources. However, there are still many problems to be solved for power LEDs for lighting: currently white LEDs generally use blue LEDs to excite yellow phosphors to synthesize white light, and there is a problem that the color rendering index of LED lamps with high color temperature is low. Since the illumination source has higher brightness requirements than the display light source, the white LED power should be as large as possible. However, during high current operation, as the working time increases, the LED itself decays, and the phosphor and packaging materials deteriorate. The cause is a decrease in luminous flux. With the large increase in power, the heat generation of the PN junction is greatly improved, and this part of the heat directly affects the operating temperature, luminous efficiency, luminescence spectrum, and lifetime reliability of the LED [4, 5]. . The performance of high-power white LED products can be improved by adjusting the ratio of phosphor to silica gel, the amount of dispensing and the amount of thermal paste, the choice of packaging materials, the design of the light distribution curve and the improvement of power conversion efficiency. Many researchers have done a lot of research on the performance of LED chips, but there are few studies on the characteristics of commercial high-power white LED lamps. Therefore, this paper studies the effects of temperature changes of different packaging materials on the color-electric properties of high-power white LED lamps.
2. Experimental procedure The object studied in this experiment is a 3W high power white LED lamp. The device includes: (1) 1W blue chip produced by Taiwan Jingyuan Optoelectronics Co., Ltd. (Specification: 45×45mil); (2) Silica gel produced by Dow Corning; (3) Hemispherical hollow lens of PC material; (4) Copper substrate (model: copper T1) and aluminum substrate (model: aluminum alloy 6063l); (5) cylindrical aluminum heat sink (specification: No. 1 Φ30mm × H47mm; No. 2 Φ45mm × H54mm); (6) Ce3+-doped Yttrium aluminum garnet (YAG) phosphor.
Figure 1 shows a schematic (a) and a cross-sectional view (b) of a high power white LED lamp. Wherein T in Figure 1(b) indicates the position of the thermocouple.
First, an automatic wire bonding machine is used to weld three chips on the aluminum substrate and the copper substrate (in a "product" type arrangement in series), and the silica gel is coated on the soldered chip to be solidified. Then, the silica gel and the YAG phosphor were mixed in a certain ratio, stirred for 10 minutes, vacuumed for 30 minutes, and then coated on the cured silica gel, wherein the curing conditions were both 150 ° C and baked for 1 h. Then, the substrate is mounted on a heat sink with a thermal paste applied therebetween. A lens and glass cover mounted on the phosphor layer can be used to control light distribution and prevent glare. When driven by a constant current source, the blue light emitted by the chip excites the phosphor, and finally a uniform white light can be seen through the lens and the glass cover.
The integrating sphere is also called a spherical photometer. It is a complete spherical shell with an inner hollow and a white diffuse reflective layer on the inner wall. The test system is calibrated with a standard halogen lamp. The light source is placed in the integrating sphere. A part of the light emitted by the light source and diffusely reflected by the spherical surface is incident on the light detector through the window on the wall of the ball. After the light is collected, the light is collected by the detector. The signal is converted into a photocurrent signal. After being sampled and amplified, it is converted into a digital signal by A/D and sent to the microprocessor. Then, the total luminous flux Φ (lm) and luminous efficiency η (lm/W) are obtained by calculation.

Kara offers a wide range of illuminated and non-illuminated Rocker Switches.Ranging from 4 to 9poles,16VA to 30 amp,with many styles of colors and functions,especially the switches with High-Current and some types which meet the industry standard IP65,IP68. Certifications include UL, CSA, TUV, CE, and more.
Middle-Sized Rocker Switches,Middle Rocker Switches,Economic Middle-Sized Rocker Switches,Universal Middle-Sized Rocker Switches
Ningbo Kara Electronic Co.,Ltd. , https://www.kara-switch.com