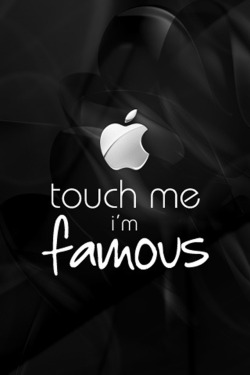
Recently, Apple CEO Tim Cook announced that from 2013, Apple will move some of its computer production lines back to the United States. With the recent trend of the "manufacturer's return to the United States", the symbolism of this move is even greater.
Behind the backflow of US manufacturing and “localized manufacturing†is the US “reindustrialization†strategy. In fact, since the beginning of the 20th century, the United States has occupied the largest share of the world's manufacturing industry for a long time. However, from the 1960s onwards, along with the trend of global industrial transfer, the United States and Europe began to de-industrialize. In the 1980s, the outsourcing of production became a major trend, and the United States turned to the service industry-based industrial structure. The hollowing out of the manufacturing industry has become increasingly prominent. Affected by this, the U.S. manufacturing industry’s share in the global manufacturing output value has been declining, falling to 21.5% in 1990, falling below 20% in 2009, and accounting for 19.4% in 2010, slightly lower than China’s 19.8%. , thus losing the status of the world's largest manufacturing output value in the past 100 years.
Since the financial crisis, the United States intends to regain the dominant right to compete in the international manufacturing industry through “reindustrializationâ€, and the strategic intention to reshape the competitive advantages of the US manufacturing industry has become even stronger. On August 11, 2010, the "Manufacturing Promotion Act" signed by Obama was regarded as the prelude to the United States launching "reindustrialization."
At present, the first major factor driving the flow of manufacturing in the United States is that the cost gap between China and the United States is shrinking. All along, the factor dividend is the first driving force for China's rapid growth. But with the revaluation of the value of China's factors, all this is changing. As China's "demographic dividend" will peak. The reversal of the labor supply and demand relationship in China will bring about a further rise in wages. Although labor costs are relatively low in these industries, the rapidly narrowing wage gap between the two countries makes it an important factor. U.S. dollar wages in China are expected to increase by 15% to 20% each year, which exceeds China's productivity growth rate. After considering the productivity of the United States, the huge labor cost gap between China's coastal areas and some of the U.S. low-cost states is expected to shrink to below 40% of current levels by 2015.
Of course, labor costs are definitely not the only factor that constitutes manufacturing costs. Since 2010, the cost of electricity in China has soared by 15%. The increase in the prices of imported thermal coal and the termination of preferential tax rates for high-energy-consuming enterprises have also pushed up the development costs of these industries, which account for 74% of China's electricity consumption. Another important cost reduction factor that cannot be overlooked is the shale gas revolution in the United States. If we consider that the decline in energy prices brought about by the shale gas revolution will drastically reduce the U.S. manufacturing costs, then this may mean that the United States will manufacture in the future. The industry is showing signs of long-term structural improvement and it is beginning to enter a rising period.
If we say that the factors of the cost gap are still only medium and long-term effects, then the key to determining the competitiveness of the manufacturing industry in China and the United States - the position in the global value chain is a more direct factor. Since the beginning of this century, the multinational companies have led the formation of the vertical division of labor in the industrial value chain and have been highly subdivided. Inter-industry division of labor, intra-industry division of labor, and intra-product division of labor have coexisted. This has promoted a new round of industrial countries. The vertical division of the industry chain has led to the division of labor, that is, multinational corporations in developed countries have occupied high-end links such as R&D and brand sales channels, and they have shifted relatively labor-intensive industries such as processing, assembly and manufacturing to developing countries.
China's manufacturing labor productivity and the value-added ratio are relatively low, equivalent to only 4.38% of the United States, 4.37% of Japan, and 5.56% of Germany. There is still a gap between the quality of China's manufacturing industry and the developed countries. From the point of view of the input contribution coefficient in the middle, the intermediate input of the value of one unit in the developed country can be roughly obtained by one unit or more of the newly created value, while China can only get a new value of creation of 0.56 units, and the value creation ability varies greatly. On the other hand, since the financial crisis in the United States, U.S. companies have reduced labor costs by reducing man-hours and reducing labor costs. Labor productivity has continued to increase. Data show that in the third quarter of this year, U.S. non-agricultural labor productivity increased at an annual rate of 4.2%. Labor productivity increased 2.9% year-on-year, far exceeding expectations.
Under the background that future low-cost advantages are unsustainable, China's manufacturing industry must establish competitiveness beyond cost leadership, and it must increase productivity to the upstream of the value chain. The pressure to increase costs has become an effective force-reversing mechanism, and has made great efforts to shift to those industrial structures with higher technological levels, increasing returns to scale, and strong industrial profitability. Of course, in the course of transformation and upgrading, "Obsolute" and "death" will make this process more painful.
Adss Fiber Optic Cable,Adss Cable Fittings,Fastening For Pole,Cable Tools For Adss
Shandong Qingguo Optical Fiber Co., Ltd. , https://www.qgfiber.com